Industrial Heat Exchangers
manufacturer, supplier, exporter in Mumbai, India
Table of Contents
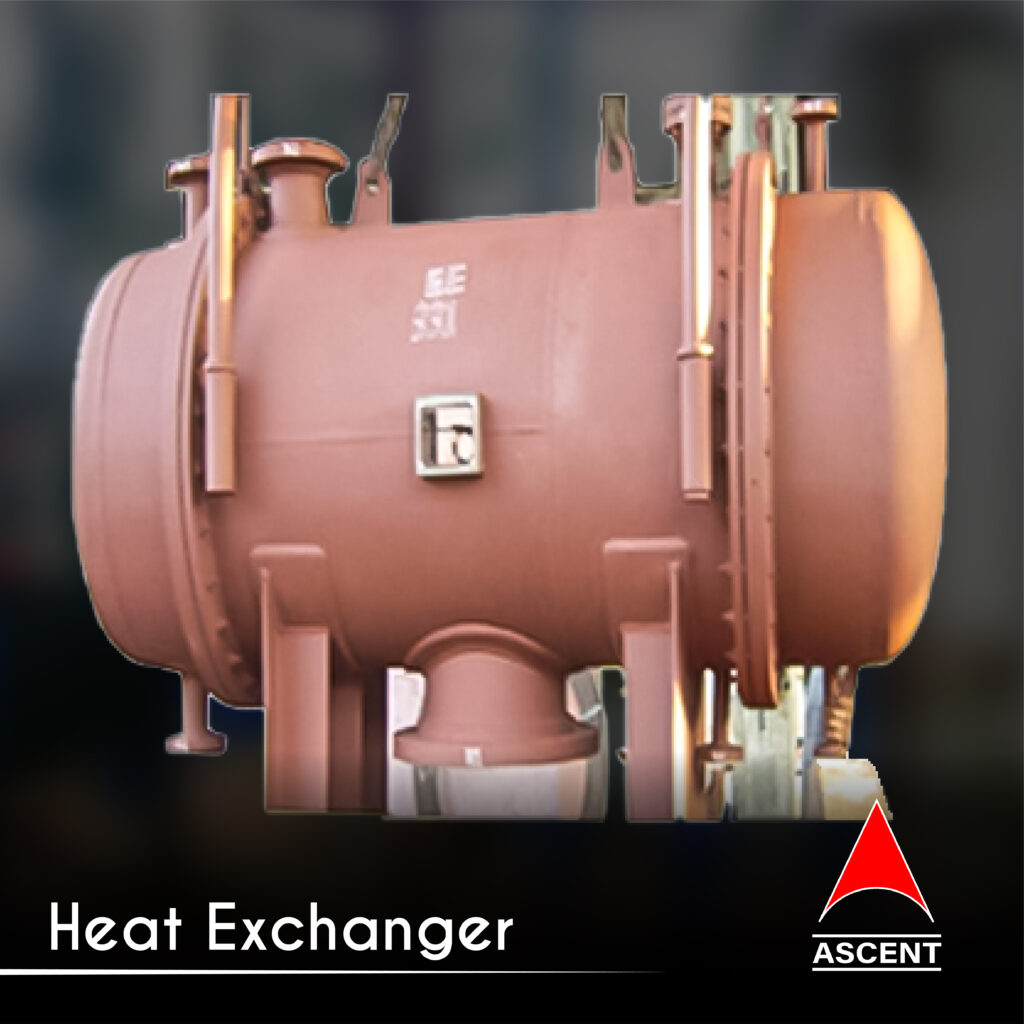
Description of Industrial Heat Exchangers
Heat exchangers are devices that transfer heat from one fluid or gas to another, without allowing them to mix. They are commonly used in industrial and residential applications, such as in air conditioning and refrigeration systems, power plants, and chemical processing plants. Industrial Heat exchangers are an essential part of many industrial processes, from power generation to food processing. They play a critical role in transferring heat from one fluid to another, either to increase or decrease the temperature of the fluids involved.
Ascent Machineries & Engg. Services produce a complete line of Heat Exchangers that are widely utilized for effective heat transfer between two fluids. These heat exchangers are categorized based on their flow arrangements, and are specially engineered to increase the wall surface area between the fluids, while minimizing resistance to fluid flow through the exchanger. Our Heat Exchangers are available in different forms and types to cater to various applications. We can supply units that comply with the standards set by ASME Sect. VIII, Sect. V, and Sect. IX of the Boiler and Pressure Vessel Code, as well as TEMA, API, HEI, and 3A Standards.
Our Industrial Heat Exchangers have a capacity range of 0.2m2 to 100.0 m2, and are made from M.S., S.S. 304, or S.S. 316 materials in a shell and tube type construction. We can also provide higher capacities as per customer requirements. Our Heat Exchangers are available in GMP construction with pre-insulated jackets and a mirror finish for API Production processes, while the standard construction is suitable for non-pharmaceutical processes.
Function of Heat Exchangers
The function of a heat exchanger is to transfer heat between two fluids while keeping them physically separate. This can be achieved in a number of ways, but the basic principle is the same: heat is transferred from a hot fluid to a cold fluid, raising the temperature of the cold fluid and lowering the temperature of the hot fluid.
Heat exchangers are used in a variety of applications, such as cooling engines in automobiles or power plants, heating or cooling process streams in chemical plants, or even in air conditioning systems to cool or heat buildings. They are also used in food processing, where heat exchangers are used to pasteurize and sterilize food products.
Types of Heat Exchangers
There are several heat exchanger examples, each with its own unique advantages and disadvantages. The most common types of heat exchangers are:
- Shell and Tube Heat Exchangers: This type of heat exchanger consists of a shell (a large pressure vessel) with a bundle of tubes inside. One fluid flows through the tubes, while the other fluid flows around the tubes in the shell. This type of heat exchanger is commonly used in power plants and chemical plants, as it can handle high pressures and temperatures.
- Tube Heat Exchanger: U Tube Heat Exchanger is a type of heat exchanger that consists of a bundle of U-shaped tubes within a cylindrical shell. One fluid flows through the inner tube while the other fluid flows through the outer shell in the opposite direction. The U Tube design allows for thermal expansion of the tubes while maintaining a constant tube length, making it ideal for high-temperature applications.
- Fin Type Heat Exchangers: A Fin Type Heat Exchanger consists of a series of fins that increase the surface area of the heat exchanger. The fins are attached to tubes, and one fluid flows through the tubes while the other fluid flows across the fins. The increased surface area allows for efficient heat transfer between the fluids. Fin Type Heat Exchangers are commonly used in applications where one of the fluids has a low heat transfer coefficient or low flow rate, as the fins help to enhance the heat transfer process. They are also commonly used in air conditioning and refrigeration systems, as they can be designed to have a compact size and high efficiency.
Features of Industrial Heat Exchangers
Industrial Heat Exchangers come with a range of features that are designed to ensure efficient heat transfer and optimal performance. Some of the key features of Industrial Heat Exchangers include:
- Durable construction materials such as stainless steel, carbon steel, or other corrosion-resistant materials.
- Various types of heat exchangers including shell and tube, U Tube Heat Exchanger, and Fin Type Heat Exchangers to suit different applications.
- Large surface area to maximize heat transfer efficiency.
- High-quality insulation to reduce heat loss and improve energy efficiency.
- Compact design to save space and facilitate easy installation and maintenance.
- High-pressure and high-temperature capabilities to handle demanding industrial processes.
- Compliance with various industry standards such as ASME Sect. VIII, Sect. V, and Sect. IX, TEMA, API, HEI, and 3A Standards.
- Customizable design to meet specific customer requirements.
Overall, Heat Exchangers are designed by industrial heat exchanger manufacturers to provide reliable and efficient heat transfer for various industrial applications while ensuring durability and optimal performance.
Heat Exchanger Industrial Applications
Heat exchangers are vital components used in various industrial processes to transfer heat between fluids, typically for heating or cooling purposes. Here are some common industrial applications of heat exchangers:
- HVAC systems: Industrial Heat exchangers are used in heating, ventilation, and air conditioning (HVAC) systems to regulate the temperature and humidity of indoor air.
- Power generation: Heat exchangers play a crucial role in power plants by transferring heat between water and steam to generate electricity.
- Chemical processing: Used in chemical processing plants to regulate the temperature of chemical reactions and maintain product quality.
- Food and beverage industry: Heat exchangers industrial are used to pasteurize milk, juice, and other food products to eliminate harmful bacteria and extend shelf life.
- Oil and gas industry: Heat exchangers are used to cool or condense gases and fluids in the production and refining of oil and gas.
- Pharmaceutical industry: Heat exchangers are used to regulate the temperature of chemical reactions in drug manufacturing and to maintain sterile environments in laboratories.
- Waste heat recovery: Heat exchangers can recover waste heat from industrial processes and reuse it for other applications, reducing energy consumption and costs.